
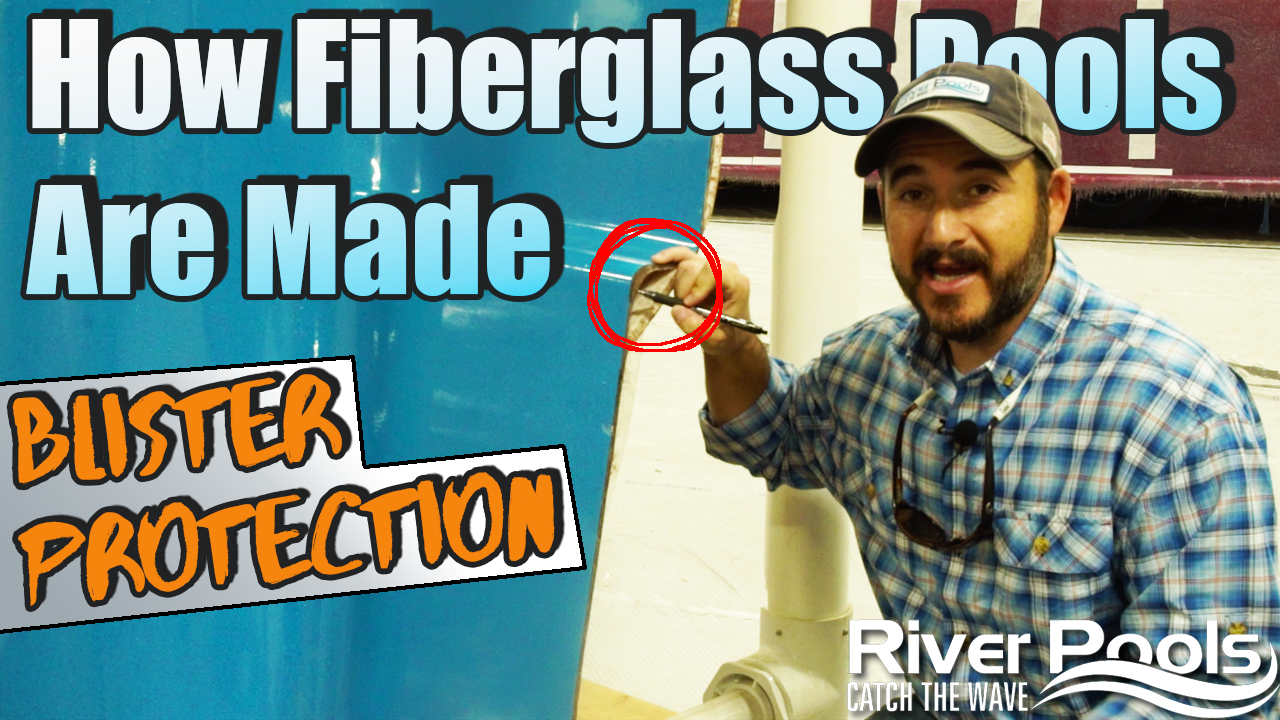
The second layer of the fiberglass pool manufacturing process is our vinyl ester chopped fiberglass layer. Vinyl ester is a premium-grade resin specifically blended to prevent an unwanted process called osmotic blistering—a phenomenon where the gelcoat surface forms actual blisters and separates from the next laminate layer.
Water travels through the gelcoat, comes in contact with other contaminants, and forms a larger molecule. The larger molecule then tries to exit the same way it came in. This causes an outward force on the gelcoat, eventually resulting in a blister.
Vinyl ester resin prevents this from happening because it acts as a watertight barrier. The water passes through the gelcoat, contacts the pure water barrier, and then leaves.
A huge variety of blended vinyl esters are available to composites manufacturers, and truth be told, it only takes a small percentage of vinyl ester to call a product “vinyl ester resin.” Our vinyl ester is specially blended to produce the best blister protection available.
A second advantage to our vinyl ester chopped fiberglass layer is that it helps drive the cure of the gelcoat. As soon as the gelcoat has set, we apply this layer of chopped fiberglass that serves as a gigantic heating blanket.
The beauty of our Cross-Lynx Composite Technology is that the exothermic heat (called exotherm for short) generated from the curing process of each layer actually helps drive the cure and cross-linking process of all previous layers. Talk about synergy!