7 Costly Sins of Fiberglass Pool Installations and How to Avoid Them
February 9th, 2010
4 min read
By Jason Hughes
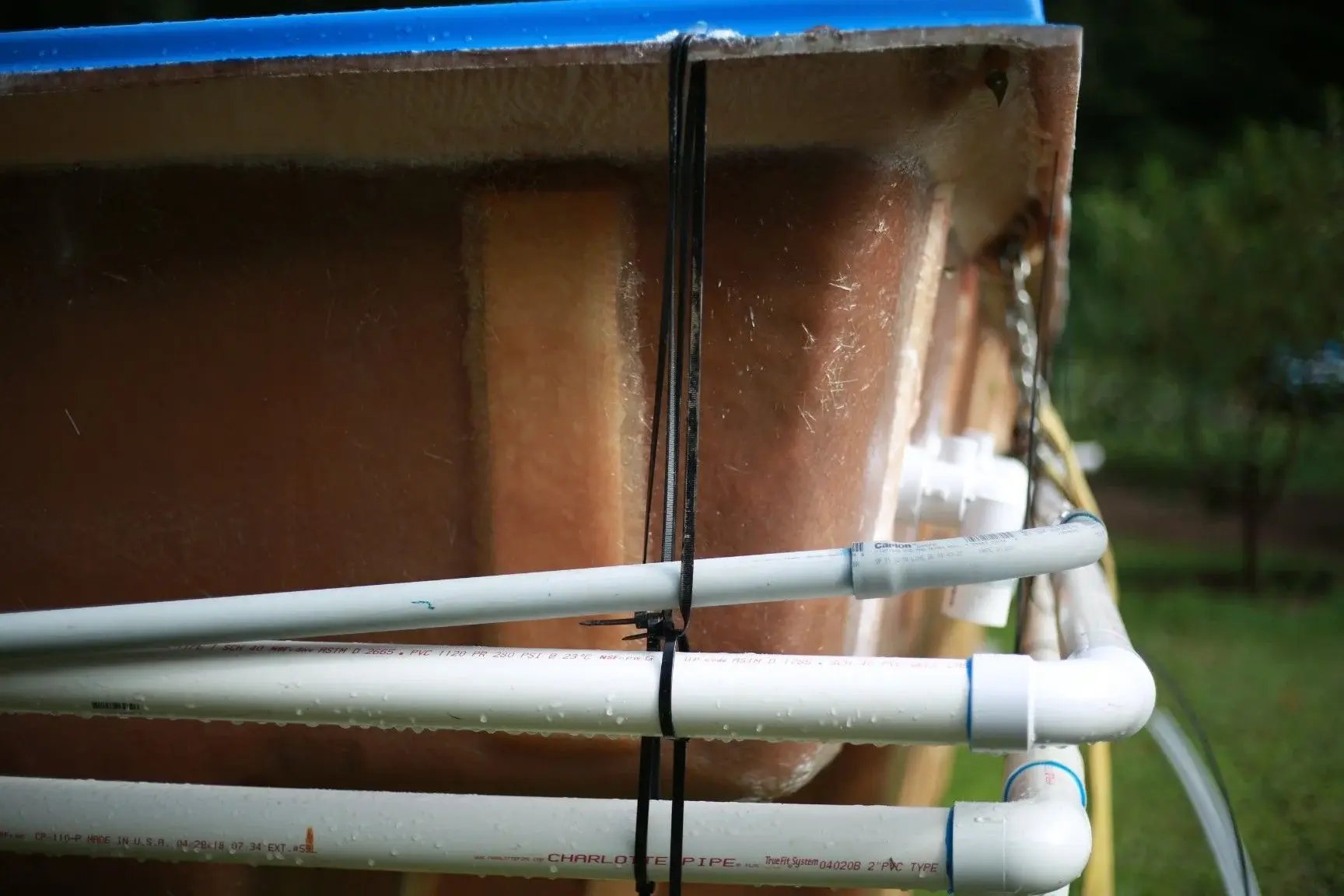
My journey in the pool industry began at 15 as a laborer for a small family-owned business, where I quickly learned that experience matters—especially when you’re sent to find a “wall stretcher” that doesn’t exist.
Since co-founding my installation company, River Pools® Virginia, in 2001, I’ve helped install over 1,000 fiberglass pools, learning firsthand what works and what doesn’t. We’ve made mistakes along the way, each one a “sin” in the world of pool installation, costing time, money, and stress. But each misstep taught us how to improve and build pools that last.
In this guide, I’ll share the 7 most common (and costly) “sins” of fiberglass pool installations so you can avoid them, whether you’re a homeowner planning a pool or a contractor looking to improve your craft.
1. Poor-Quality Cantilevered Concrete Coping in Fiberglass Pools
No matter how well a pool is installed, poor cantilevered concrete coping can ruin the look and longevity of your project. We learned this the hard way, and over time, we developed clear best practices for securing forms and placing concrete to ensure a smooth, durable finish.
Key best practices:
- Use double the ties recommended by the form manufacturer.
- Use tape to support bends and tight corners.
- Tap the forms to vibrate the concrete and bring cream to the surface for a smooth finish.
For a deeper dive, check out our guide: Why Pouring Concrete Coping Around a Fiberglass Pool Is So Difficult.
2. Skipping a Dewatering System in a Fiberglass Pool Installation
A dewatering system prevents hydrostatic pressure damage by allowing groundwater to be removed before draining a pool. Without it, water pressure outside the shell can damage the pool if there’s less water inside than outside.
Best practice: We install an 8-inch PVC pipe encased in gravel during the install, providing easy access for a pump if groundwater removal is needed. It costs under $100 and can save you thousands down the road.
Learn how hydrostatic pressure affects fiberglass pools.
3. Poor Plumbing Practices Around Fiberglass Pools
We often see three critical plumbing mistakes:
- Not pressure testing lines before pouring the patio.
- Failing to secure the plumbing to prevent settlement.
Best practice: Heat-bend rigid PVC to contour the pool while maintaining strength, and secure plumbing to the pool shell with cables to prevent future settlement.
And if the pool needs to be drained? Simply remove the skimmer lid, drop a pump down the pipe, and pump the groundwater out.
This costs a couple of hundred dollars, max, per pool, and frankly, is a step that a pool contractor can’t afford to miss.
4. Using Sand as Base and Backfill Material
While sand is viewed as an acceptable material by many installers and some manufacturers, it liquefies when saturated, leading to:
- Settlement of the pool shell.
- Bulging pool walls.
- Plumbing settlement and leaks.
Best practice: Use clean crushed gravel as backfill. It compacts immediately, won’t shift when wet, and prevents plumbing issues and wall bulging.
Want to talk to an independent installation company about a possible pool project for your backyard? Click the button below and we'll help you get connected.
- River Pools Manufacturing
5. Ignoring Step and Wall Support During Installation
Fiberglass steps and benches can sag over time without proper support. Similarly, straight pool walls can bow without proper monitoring.
Best practice:
- Use CMU blocks to support steps or tanning ledges while pouring concrete under them during installation to keep them level.
- Use a string line to check wall alignment during backfilling, adjusting as needed to prevent bowing.
6. Building Up Patios with Loose Dirt
Using loose dirt to build up a patio is a recipe for future settlement and cracking.
Best practice: Use a turn-down slab where the concrete extends to ground level, creating a stable, lasting support for the patio even on sloped yards.
7. Improper Pool Leveling Methods
The only way to ensure a fiberglass pool is level long-term is to set it right the first time. Adding material under a pool to adjust its level often leads to uneven settling.
Best practice: Take the time to set and level the pool correctly upon initial placement, ensuring it rests on a stable, undisturbed foundation.
Frequently Asked Questions About Fiberglass Pool Installations
What is the best base material for a fiberglass pool?
The best base material for a fiberglass pool is clean crushed gravel. It compacts immediately, won't shift when wet, and prevents issues like wall bulging and plumbing settlement.
Do I need a dewatering system for my fiberglass pool?
Yes, a dewatering system helps prevent hydrostatic pressure damage by allowing you to remove groundwater before draining your pool, protecting your investment long-term.
Is flexible PVC good for fiberglass pool plumbing?
No, flexible PVC is not recommended for underground use despite its popularity. Rigid PVC, heat-bent to contour the pool, is stronger and more durable for fiberglass pool plumbing.
How can I avoid settlement under my pool patio?
Avoid using loose dirt to build up patios. Instead, use a turn-down slab so the concrete extends to ground level, providing a stable, long-lasting base that prevents settlement and cracking.
Why is proper pool leveling important?
Proper leveling ensures your fiberglass pool stays stable over time. Adjusting the level after placement can lead to uneven settling, so it's critical to set it correctly on a stable foundation during initial installation.
Conclusion: Avoid These Sins to Build a Lasting Fiberglass Pool
These seven “sins” are costly mistakes that we’ve learned to avoid through experience. By understanding and addressing these areas, you can protect your investment and ensure your fiberglass pool project is built to last.
If you’re planning a fiberglass pool project, connect with a River Pools builder to get expert guidance and ensure your pool installation is done right.
About the Author
Jason Hughes, Co-Owner of River Pools® Virginia and Genesis Instructor
Since co-founding River Pools Virginia in 2001, Jason Hughes has overseen the installation of over 1,000 fiberglass pools, refining best practices that are now industry standards. As a Genesis instructor, he trains professionals nationwide to improve pool installation quality, helping homeowners get pools that last.
Learn more about Jason and his work here.
From the Manufacturer
At River Pools, we design and manufacture fiberglass pool shells, but we care just as much about how those pools are installed. That’s why we fully endorse fiberglass pool installation practices grounded in real-world experience and proven results.
Many of the methods described in this article, like gravel backfill and supported plumbing, are now taught in top certification programs like Genesis by PHTA. We encourage homeowners to choose builders who stay current with evolving standards and who share our commitment to long-term pool performance.
Editor's note: This blog article was updated on July 3, 2025.
Up Next:
7 Clues Your Pool Builder Has It Together
The Ultimate Swimming Pool Builder Vetting Checklist
Jason Hughes is a partner at River Pools Virginia, a fiberglass pool installation company based in Warsaw, Virginia. With over 20 years of hands-on experience, Jason has dedicated his career to helping families create beautiful, functional backyards while ensuring every fiberglass pool installation meets the highest standards of quality and safety. In addition to his work with homeowners, Jason serves as a GENESIS instructor with the Pool & Hot Tub Alliance (PHTA), where he teaches fiberglass pool installation best practices to pool professionals across the country. Whether he’s on a job site or leading a training session, Jason is passionate about raising the bar for fiberglass pool installations and helping families make confident, informed decisions as they transform their outdoor spaces.
Topics: